
Understanding Raw Materials, Their Types, and Management Tips
Sovia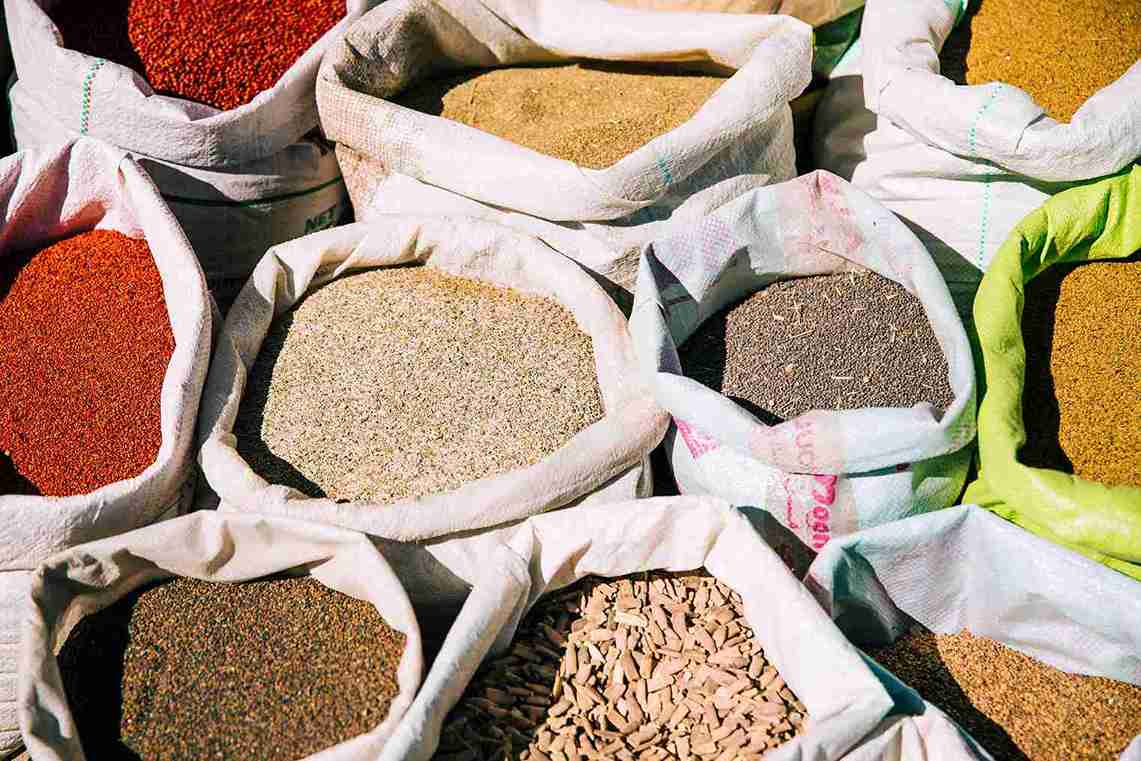
Every industry requires raw materials to produce high-quality products. However, many businesses still face challenges in managing raw material inventory effectively.
Sourcing raw materials close to the production site can help reduce operational costs, while poor management can lead to wastage. Let's explore raw materials and how to manage them efficiently in this article!
What Are Raw Materials?
Raw materials are the primary materials used to create a product through an industrial production process.
These materials are prominently visible in the finished product and make up the largest part of its composition. Choosing raw materials carefully is crucial, as their quality significantly affects the final product outcome.
Besides primary materials, there are also auxiliary materials that support the production process.
All these materials must be managed properly to ensure smooth and efficient production.
Sourcing raw materials close to the production site can help lower operational costs, including shipping and storage expenses.
In the manufacturing industry, raw materials cannot be used directly without undergoing specific processing steps.
The process that transforms raw materials into another form is known as production.
Therefore, proper raw material management is essential to ensure efficiency and maintain product quality.
Read more: 5 Best Inventory Valuation Methods to Optimize Your Business!
Types of Raw Materials
Source: freepik.com
Raw materials are generally categorized into two main types: direct materials and indirect materials. Let’s take a closer look at each type!
1. Direct Material
Direct materials are the primary materials used in producing a product. Without these materials, the final product cannot be formed. Examples include wood in furniture manufacturing or wheat in flour production.
The cost of direct materials usually correlates with the number of products produced. If costs are high but production output does not match, there may be issues in the production process.
2. Indirect Material
Indirect materials support production but are not visibly present in the final product. For instance, in furniture manufacturing, wood is a direct material, whereas nails and primer paint are indirect materials.
Although not visible, indirect materials are essential for smooth production. Therefore, procurement planning must be done carefully.
Apart from direct and indirect materials, raw materials can also be classified into five additional categories:
1) Raw Materials
The main production materials in their raw form, sourced from nature, suppliers, or produced independently.
2) Purchased Parts/Components
Pre-made parts or components that are ready for assembly into the final product, such as screws or hinges in furniture.
3) Supplies
Materials used in production but not part of the final product, such as machine lubricants.
4) Work in Process
Products still in the production stage that require further processing before completion.
5) Finished Goods
Products that have completed the production process and are ready for sale or delivery to customers.
Tips for Managing Raw Material Inventory
Proper raw material inventory management can improve efficiency and reduce the risk of losses. Here are five tips you can apply:
1. Avoid Overstock and Understock
Excess or insufficient stock can hinder operations. Overstocking may indicate an overly optimistic sales forecast, while understocking may result from inaccurate demand forecasting or supply chain disruptions. Always evaluate sales and demand data.
2. Set Reorder Points for Safety Stock
Don’t wait until stock runs out before reordering. Calculate reorder points to determine when to replenish inventory. This ensures smooth production without overloading storage with excess stock.
3. Use a Material Resource Planning System
This system helps determine the types and quantities of raw materials needed. By analyzing historical consumption data and future forecasts, you can optimize stock levels.
Additionally, it speeds up the production process while reducing the risk of material shortages.
4. Ensure Quality Control
Poor-quality raw materials can slow down production and increase labor costs. Always conduct quality checks before using materials.
Partnering with reliable vendors can also minimize the risk of receiving substandard materials.
5. Automate Data Management
Managing inventory manually is time-consuming and prone to errors. Use software to help with demand forecasting, supply chain data analysis, and production cost determination.
If your business is in the food and beverage sector, a raw material tracking system can help maintain quality standards.
Read more: 9 Ways to Create Inventory Reports for Restaurants and Culinary Businesses
Conclusion
Raw materials are a crucial factor in the production process and must be managed properly.
Choosing the right suppliers, implementing an effective inventory management system, and planning production carefully will help improve business efficiency.
If you want to optimize raw material management, ESB Goods offers the best solution. With an integrated supply chain management system, the procurement-to-payment process is directly connected with trusted suppliers.
Optimize your business with the best raw material management solution! Call ESB Team now!
